La electrificación y la automatización se han desarrollado rápidamente en China.Los disyuntores de caja moldeada (MCCB) se han utilizado ampliamente por sus buenas funciones de protección contra sobrecargas y cortocircuitos.
1.Background:
La electrificación y la automatización se han desarrollado rápidamente en China.Los disyuntores de caja moldeada (MCCB) se han utilizado ampliamente por sus buenas funciones de protección contra sobrecargas y cortocircuitos. Los MCCB, como los aparatos de protección más básicos, cuentan con una amplia aplicación, una amplia gama de variedades y una estructura compacta y complicada. En el pasado, los diseñadores y productores de aparatos eléctricos a menudo se veían en la necesidad de fabricar piezas prototipo a través del procesamiento de recubrimiento de silicona y el procesamiento CNC, y llevar a cabo verificaciones y pruebas en la etapa de diseño y desarrollo de nuevos productos, lo que requeriría un largo ciclo de procesamiento y altos costos, y se convertiría en un problema importante si se necesitaran desarrollar docenas o cientos de nuevos productos cada año. A continuación se presenta un caso con un cliente final de TPM3D.
2.Perfil del cliente:
El cliente es un proveedor de soluciones de energía inteligente de renombre mundial, y sus productos incluyen distribuidores de energía, aparatos terminales, control de motores y dispositivos de protección, automatización industrial, etc. Con ventas anuales que superan los RMB 80 mil millones, la compañía opera en más de 140 países y regiones. Este cliente combina el sistema de sinterización láser TPM3D P360 con PPS para su I + D y producción de prueba de varios aparatos eléctricos de bajo voltaje.
3. Desarrollo del producto:
El cliente desarrolla y produce más de 10.000 nuevas piezas de productos eléctricos cada año. En la actualidad, sus principales productos impresos con TPM3D P360 incluyen cajas para disyuntores de caja moldeada y otras piezas estructurales.
Después de imprimir la muestra, el cliente realizará la verificación del ensamblaje y las pruebas funcionales. Se requiere la precisión de la verificación del ensamblaje para alcanzar ±0.2 mm. Las pruebas funcionales incluyen principalmente: prueba de resistencia, prueba de retardo largo, prueba de aislamiento, etc. El material adoptado es 30% nylon reforzado con cuentas de vidrio 12 (Precimid1172Pro GF30) de TMP3D, que cuenta con una excelente resistencia y resistencia al impacto. Según el cliente, los materiales pueden cumplir con los requisitos de prueba en términos de propiedades mecánicas y aislamiento. Además, la temperatura de deformación térmica del material alcanza los 184,4 ° C, y las cajas impresas se pueden probar sin deformarse en un termostato a 80 ° C durante 4 horas, lo que cumple con los requisitos de la prueba de largo retardo. En general, las cajas de disyuntores de caja moldeada impresas con tecnología SLS están a la par con las piezas moldeadas por inyección tradicionales.
4.Respetuoso con el medio ambiente:
Al comprar el sistema de sinterización láser P360, el cliente también configuró una estación de procesamiento de piezas y polvo (PPS), que lanzada en 2018 por TPM3D, la primera en Asia, integró la limpieza de piezas, el reciclaje de polvo, la mezcla, la alimentación y la recolección de polvo, resolvió los problemas como la pérdida de tiempo, la contaminación y la seguridad al operar mano de obra. PPS ha pasado el estándar nacional para la zona 22 a prueba de explosiones de polvo y la certificación ce internacional y obtuvo un alto reconocimiento por su mejor desempeño para garantizar la seguridad del usuario.
5.Reducción de costes y mejora de la eficiencia:
Antes de introducir el sistema de impresión 3D SLS, el cliente adoptó el mecanizado CNC o el mecanizado de recubrimiento de silicona subcontratado, que tardó al menos 5-6 días en obtener las piezas de prueba. Después de que el sistema de sinterización láser P360 se puso en producción, las muestras se pudieron obtener y probar después de solo 48 horas, ahorrando tiempo en más del 60%. En el pasado, el procesamiento de casos subcontratado costaba alrededor de RMB 4,000 / conjunto. Con la tecnología de impresión 3D SLS, el costo se puede controlar bajo RMB 700 / set, una reducción de más del 80%. Con una alta tasa de utilización, actualmente el equipo del cliente puede imprimir 2-3 cámaras completas por semana en promedio. Además, según el cliente, puede ahorrar alrededor de RMB 700,000 por año, reduciendo así mejor los costos y mejorando la eficiencia.
Comparación de costo y ciclo entre el proceso tradicional y el proceso de impresión 3D SLS:
"El sistema P360 de TPM3D es conveniente y rápido; PPS reduce la intervención manual al tiempo que logra una alta eficiencia de procesamiento de piezas y polvo. La solución ahorra tiempo y costes y garantiza el orden y la seguridad del medio ambiente".
——Comentarios del cliente
La electrificación y la automatización se han desarrollado rápidamente en China.Los disyuntores de caja moldeada (MCCB) se han utilizado ampliamente por sus buenas funciones de protección contra sobrecargas y cortocircuitos. Los MCCB, como los aparatos de protección más básicos, cuentan con una amplia aplicación, una amplia gama de variedades y una estructura compacta y complicada. En el pasado, los diseñadores y productores de aparatos eléctricos a menudo se veían en la necesidad de fabricar piezas prototipo a través del procesamiento de recubrimiento de silicona y el procesamiento CNC, y llevar a cabo verificaciones y pruebas en la etapa de diseño y desarrollo de nuevos productos, lo que requeriría un largo ciclo de procesamiento y altos costos, y se convertiría en un problema importante si se necesitaran desarrollar docenas o cientos de nuevos productos cada año. A continuación se presenta un caso con un cliente final de TPM3D.
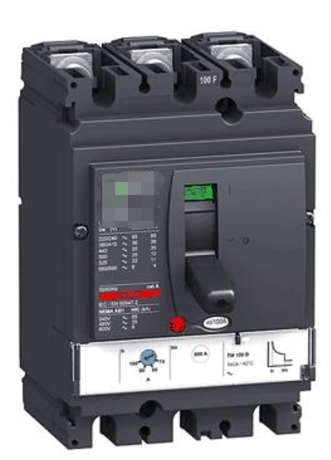
Un tipo de disyuntor de caja moldeada
2.Perfil del cliente:
El cliente es un proveedor de soluciones de energía inteligente de renombre mundial, y sus productos incluyen distribuidores de energía, aparatos terminales, control de motores y dispositivos de protección, automatización industrial, etc. Con ventas anuales que superan los RMB 80 mil millones, la compañía opera en más de 140 países y regiones. Este cliente combina el sistema de sinterización láser TPM3D P360 con PPS para su I + D y producción de prueba de varios aparatos eléctricos de bajo voltaje.

Sistema de sinterización láser TPM3D P360 + PPS
3. Desarrollo del producto:
El cliente desarrolla y produce más de 10.000 nuevas piezas de productos eléctricos cada año. En la actualidad, sus principales productos impresos con TPM3D P360 incluyen cajas para disyuntores de caja moldeada y otras piezas estructurales.

disyuntor de caja moldeada desarrollado por LA TECNOLOGÍA SLS
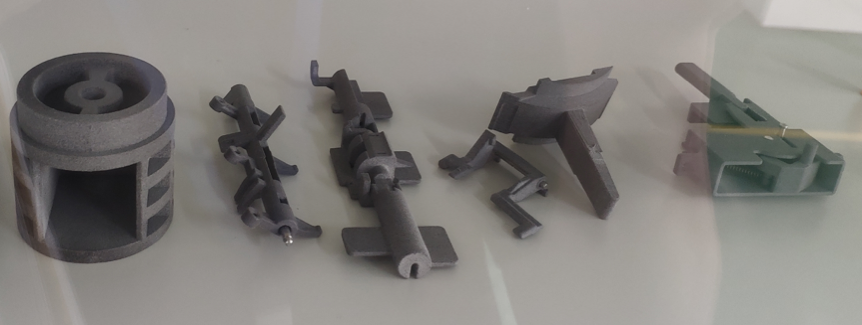
Otras partes estructurales
Después de imprimir la muestra, el cliente realizará la verificación del ensamblaje y las pruebas funcionales. Se requiere la precisión de la verificación del ensamblaje para alcanzar ±0.2 mm. Las pruebas funcionales incluyen principalmente: prueba de resistencia, prueba de retardo largo, prueba de aislamiento, etc. El material adoptado es 30% nylon reforzado con cuentas de vidrio 12 (Precimid1172Pro GF30) de TMP3D, que cuenta con una excelente resistencia y resistencia al impacto. Según el cliente, los materiales pueden cumplir con los requisitos de prueba en términos de propiedades mecánicas y aislamiento. Además, la temperatura de deformación térmica del material alcanza los 184,4 ° C, y las cajas impresas se pueden probar sin deformarse en un termostato a 80 ° C durante 4 horas, lo que cumple con los requisitos de la prueba de largo retardo. En general, las cajas de disyuntores de caja moldeada impresas con tecnología SLS están a la par con las piezas moldeadas por inyección tradicionales.
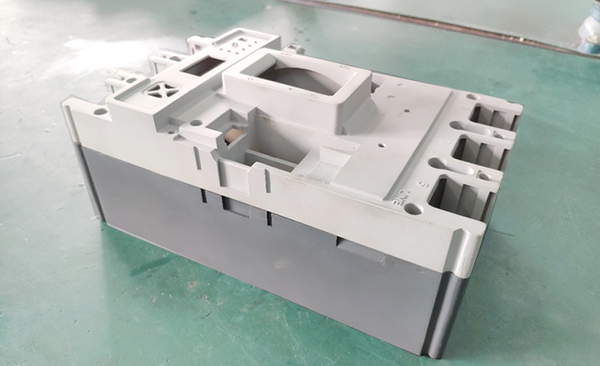
Verificación de ensamblaje
4.Respetuoso con el medio ambiente:
Al comprar el sistema de sinterización láser P360, el cliente también configuró una estación de procesamiento de piezas y polvo (PPS), que lanzada en 2018 por TPM3D, la primera en Asia, integró la limpieza de piezas, el reciclaje de polvo, la mezcla, la alimentación y la recolección de polvo, resolvió los problemas como la pérdida de tiempo, la contaminación y la seguridad al operar mano de obra. PPS ha pasado el estándar nacional para la zona 22 a prueba de explosiones de polvo y la certificación ce internacional y obtuvo un alto reconocimiento por su mejor desempeño para garantizar la seguridad del usuario.

ambiente limpio y ordenado
5.Reducción de costes y mejora de la eficiencia:
Antes de introducir el sistema de impresión 3D SLS, el cliente adoptó el mecanizado CNC o el mecanizado de recubrimiento de silicona subcontratado, que tardó al menos 5-6 días en obtener las piezas de prueba. Después de que el sistema de sinterización láser P360 se puso en producción, las muestras se pudieron obtener y probar después de solo 48 horas, ahorrando tiempo en más del 60%. En el pasado, el procesamiento de casos subcontratado costaba alrededor de RMB 4,000 / conjunto. Con la tecnología de impresión 3D SLS, el costo se puede controlar bajo RMB 700 / set, una reducción de más del 80%. Con una alta tasa de utilización, actualmente el equipo del cliente puede imprimir 2-3 cámaras completas por semana en promedio. Además, según el cliente, puede ahorrar alrededor de RMB 700,000 por año, reduciendo así mejor los costos y mejorando la eficiencia.
Comparación de costo y ciclo entre el proceso tradicional y el proceso de impresión 3D SLS:
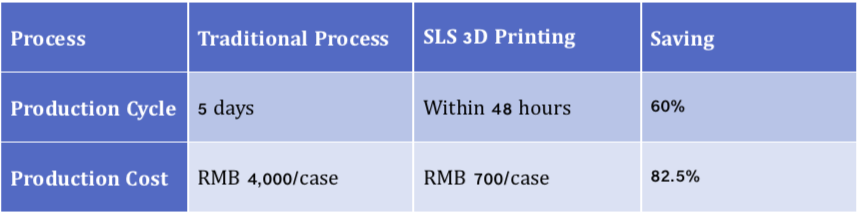
"El sistema P360 de TPM3D es conveniente y rápido; PPS reduce la intervención manual al tiempo que logra una alta eficiencia de procesamiento de piezas y polvo. La solución ahorra tiempo y costes y garantiza el orden y la seguridad del medio ambiente".
——Comentarios del cliente