L’électrification et l’automatisation se sont développées rapidement en Chine.Les disjoncteurs à boîtier moulé (MCCB) ont été largement utilisés pour leurs bonnes fonctions de protection contre les surcharges et les courts-circuits.
1.Contexte :
L’électrification et l’automatisation se sont développées rapidement en Chine.Les disjoncteurs à boîtier moulé (MCCB) ont été largement utilisés pour leurs bonnes fonctions de protection contre les surcharges et les courts-circuits. Les MCCB, en tant qu’appareils de protection les plus élémentaires, présentent une application étendue, une large gamme de variétés et une structure compacte et compliquée. Dans le passé, les concepteurs et les producteurs d’appareils électriques ont souvent jugé nécessaire de fabriquer des pièces prototypes par traitement de revêtement de silicone et traitement CNC, et d’effectuer des vérifications et des tests au stade de la conception et du développement de nouveaux produits, ce qui nécessiterait un long cycle de traitement et des coûts élevés, et deviendrait un problème majeur si des dizaines ou des centaines de nouveaux produits devaient être développés chaque année. Vous trouverez ci-dessous un cas avec un client final de TPM3D.
2.Profil du client :
Le client est un fournisseur de solutions énergétiques intelligentes de renommée mondiale, et ses produits comprennent des distributeurs d’énergie, des appareils terminaux, des appareils de contrôle et de protection des moteurs, de l’automatisation industrielle, etc. Avec un chiffre d’affaires annuel supérieur à 80 milliards de RMB, la société opère dans plus de 140 pays et régions. Ce client combine le système de frittage laser TPM3D P360 avec PPS pour sa R&D et la production d’essai de divers appareils électriques basse tension.
3.Développement de produits:
Le client développe et produit plus de 10 000 nouvelles pièces de produits électriques chaque année. À l’heure actuelle, ses principaux produits imprimés avec TPM3D P360 comprennent des boîtiers pour disjoncteurs à boîtier moulé et d’autres pièces structurelles.
Une fois l’échantillon imprimé, le client effectuera une vérification de l’assemblage et des tests fonctionnels. La précision de la vérification de l’assemblage doit atteindre ±0,2 mm. Les tests fonctionnels comprennent principalement: test de résistance, test de retard long, test d’isolation, etc. Le matériau adopté est le nylon 12 renforcé de billes de verre à 30% (Precimid1172Pro GF30) de TMP3D, qui présente une excellente résistance et résistance aux chocs. Selon le client, les matériaux peuvent répondre aux exigences de test en termes de propriétés mécaniques et d’isolation. De plus, la température de déformation thermique du matériau atteint jusqu’à 184,4 ° C et les boîtiers imprimés peuvent être testés sans être déformés dans un thermostat à 80 ° C pendant 4 heures, ce qui répond aux exigences du test à long délai. Dans l’ensemble, les boîtiers de disjoncteurs à boîtier moulé imprimés avec la technologie SLS sont comparables aux pièces moulées par injection traditionnelles.
4.Respectueux de l’environnement:
Lors de l’achat du système de frittage laser P360, le client a également configuré une station de traitement des pièces et des poudres (PPS), lancée en 2018 par TPM3D, la première en Asie, intégrant le nettoyage des pièces, le recyclage de la poudre, le mélange, l’alimentation et la collecte de poudre, résolvant les problèmes tels que la perte de temps, la pollution et la sécurité lors de l’opération de main-d’œuvre. PPS a passé la norme nationale pour la zone antidéflagrante de poussière 22 et la certification internationale CE et a obtenu une haute reconnaissance pour ses meilleures performances en matière de sécurité des utilisateurs.
5.Réduction des coûts et amélioration de l’efficacité :
Avant d’introduire le système d’impression 3D SLS, le client a adopté l’usinage CNC ou l’usinage externalisé du revêtement en silicone, ce qui a pris au moins 5 à 6 jours pour obtenir les pièces de test. Après la mise en production du système de frittage laser P360, les échantillons ont pu être obtenus et testés après seulement 48 heures, ce qui a permis de gagner du temps de plus de 60%. Dans le passé, le traitement des cas externalisé coûtait environ 4 000 RMB / ensemble. Avec la technologie d’impression 3D SLS, le coût peut être contrôlé sous RMB 700 / set, soit une réduction de plus de 80%. Avec un taux d’utilisation élevé, l’équipement du client peut actuellement imprimer 2 à 3 chambres complètes par semaine en moyenne. En outre, selon le client, il peut économiser environ 700 000 RMB par an, réduisant ainsi mieux les coûts et améliorant l’efficacité.
Comparaison du coût et du cycle entre le processus traditionnel et le processus d’impression 3D SLS:
« Le système P360 de TPM3D est pratique et rapide ; PpS réduit l’intervention manuelle tout en atteignant une efficacité de traitement élevée des pièces et de la poudre. La solution permet d’économiser du temps et de l’argent et d’assurer la propreté et la sécurité de l’environnement. »
——Commentaires du client
L’électrification et l’automatisation se sont développées rapidement en Chine.Les disjoncteurs à boîtier moulé (MCCB) ont été largement utilisés pour leurs bonnes fonctions de protection contre les surcharges et les courts-circuits. Les MCCB, en tant qu’appareils de protection les plus élémentaires, présentent une application étendue, une large gamme de variétés et une structure compacte et compliquée. Dans le passé, les concepteurs et les producteurs d’appareils électriques ont souvent jugé nécessaire de fabriquer des pièces prototypes par traitement de revêtement de silicone et traitement CNC, et d’effectuer des vérifications et des tests au stade de la conception et du développement de nouveaux produits, ce qui nécessiterait un long cycle de traitement et des coûts élevés, et deviendrait un problème majeur si des dizaines ou des centaines de nouveaux produits devaient être développés chaque année. Vous trouverez ci-dessous un cas avec un client final de TPM3D.
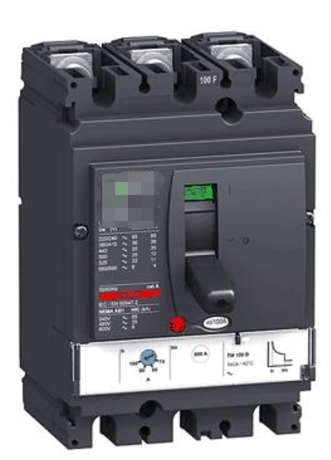
Un type de disjoncteur à boîtier moulé
2.Profil du client :
Le client est un fournisseur de solutions énergétiques intelligentes de renommée mondiale, et ses produits comprennent des distributeurs d’énergie, des appareils terminaux, des appareils de contrôle et de protection des moteurs, de l’automatisation industrielle, etc. Avec un chiffre d’affaires annuel supérieur à 80 milliards de RMB, la société opère dans plus de 140 pays et régions. Ce client combine le système de frittage laser TPM3D P360 avec PPS pour sa R&D et la production d’essai de divers appareils électriques basse tension.

Système de frittage laser TPM3D P360 +PPS
3.Développement de produits:
Le client développe et produit plus de 10 000 nouvelles pièces de produits électriques chaque année. À l’heure actuelle, ses principaux produits imprimés avec TPM3D P360 comprennent des boîtiers pour disjoncteurs à boîtier moulé et d’autres pièces structurelles.

disjoncteur à boîtier moulé développé par la technologie SLS
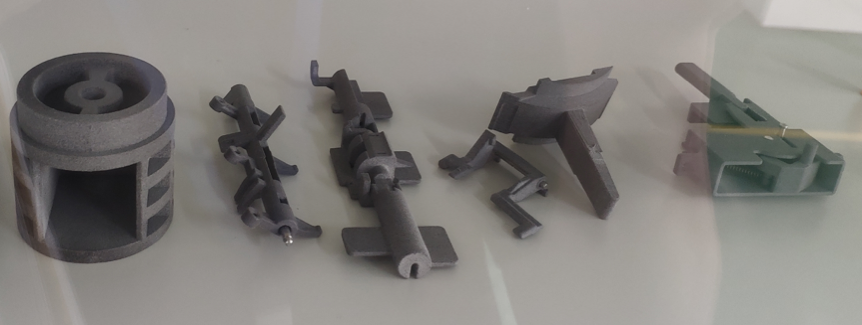
Autres pièces structurelles
Une fois l’échantillon imprimé, le client effectuera une vérification de l’assemblage et des tests fonctionnels. La précision de la vérification de l’assemblage doit atteindre ±0,2 mm. Les tests fonctionnels comprennent principalement: test de résistance, test de retard long, test d’isolation, etc. Le matériau adopté est le nylon 12 renforcé de billes de verre à 30% (Precimid1172Pro GF30) de TMP3D, qui présente une excellente résistance et résistance aux chocs. Selon le client, les matériaux peuvent répondre aux exigences de test en termes de propriétés mécaniques et d’isolation. De plus, la température de déformation thermique du matériau atteint jusqu’à 184,4 ° C et les boîtiers imprimés peuvent être testés sans être déformés dans un thermostat à 80 ° C pendant 4 heures, ce qui répond aux exigences du test à long délai. Dans l’ensemble, les boîtiers de disjoncteurs à boîtier moulé imprimés avec la technologie SLS sont comparables aux pièces moulées par injection traditionnelles.
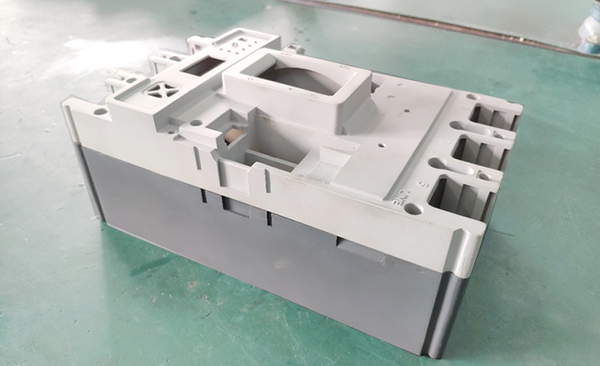
Vérification de l’assemblage
4.Respectueux de l’environnement:
Lors de l’achat du système de frittage laser P360, le client a également configuré une station de traitement des pièces et des poudres (PPS), lancée en 2018 par TPM3D, la première en Asie, intégrant le nettoyage des pièces, le recyclage de la poudre, le mélange, l’alimentation et la collecte de poudre, résolvant les problèmes tels que la perte de temps, la pollution et la sécurité lors de l’opération de main-d’œuvre. PPS a passé la norme nationale pour la zone antidéflagrante de poussière 22 et la certification internationale CE et a obtenu une haute reconnaissance pour ses meilleures performances en matière de sécurité des utilisateurs.

environnement propre et bien rangé
5.Réduction des coûts et amélioration de l’efficacité :
Avant d’introduire le système d’impression 3D SLS, le client a adopté l’usinage CNC ou l’usinage externalisé du revêtement en silicone, ce qui a pris au moins 5 à 6 jours pour obtenir les pièces de test. Après la mise en production du système de frittage laser P360, les échantillons ont pu être obtenus et testés après seulement 48 heures, ce qui a permis de gagner du temps de plus de 60%. Dans le passé, le traitement des cas externalisé coûtait environ 4 000 RMB / ensemble. Avec la technologie d’impression 3D SLS, le coût peut être contrôlé sous RMB 700 / set, soit une réduction de plus de 80%. Avec un taux d’utilisation élevé, l’équipement du client peut actuellement imprimer 2 à 3 chambres complètes par semaine en moyenne. En outre, selon le client, il peut économiser environ 700 000 RMB par an, réduisant ainsi mieux les coûts et améliorant l’efficacité.
Comparaison du coût et du cycle entre le processus traditionnel et le processus d’impression 3D SLS:
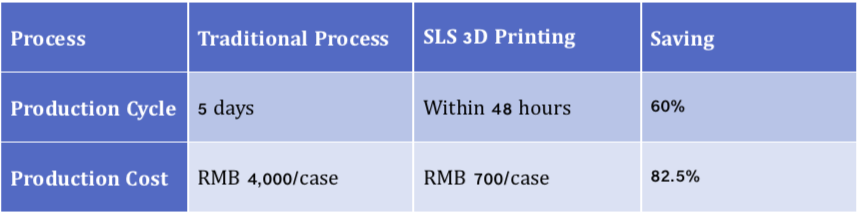
« Le système P360 de TPM3D est pratique et rapide ; PpS réduit l’intervention manuelle tout en atteignant une efficacité de traitement élevée des pièces et de la poudre. La solution permet d’économiser du temps et de l’argent et d’assurer la propreté et la sécurité de l’environnement. »
——Commentaires du client