As we all know, with the rapid development of the third industrial revolution as well as continuous reform and innovation of product technology, there are more and more requirements on manufacturing and material performance.
TPM3D is the only 3D printing manufacturer in the Greater China region with TUV (CE) certification from TUV Rheinland. It understands the application needs of end users and wins universal praises of all the users regardless of the printing stability and product superiority of SLS equipment, or the material requirements on product design performance, especially in terms of prototype manufacturers, it can bring direct benefits for the customers with about 50% less of the printing costs.
Some people may wonder how the cost of expensive prototype manufacturing be greatly reduced. Now, we’d like to make detailed explanation as follows!
First Efficiency: Equipment ---- Space efficiency
Firstly, with nearly 20 years of prototype service experience and technology, TPM3D can meet the customer's economic efficiency as much as possible during the continuous equipment improvement. Due to compact equipment structure, the cost of occupied space will be greatly reduced. The main host only takes 2.6m2of area, compared to the 3.7m2 of space occupation of other similar products. In China where factory space is very expensive, the cost of equipment space occupation is also an issue worth of being considered.
Second Efficiency: Powder Feeding ---- Time Efficiency
As for the design of powder feeding of sintering device, the mode of bilateral powder feeding with scrapers is adopted, which not only shortens the speed of powder feeding, but also saves the consumption of nitrogen as well as electricity. The oxidation rate of materials in high temperature environment has also be reduced to make powder quality more stable and less costs of use.
Third Efficiency: Scanning ---- Labor Efficiency
Due to Iradion Laser CO2, the scanning speed of TPM3D equipment can reach 15 m/s while the products of other brands can only reach 10 m/s and the light spot diameter can reach 0.3mm. With the built-in structure for constant temperature in same chamber, it can perform online compensation in single-point temperature detection while increasing powder heating speed. In addition, the TPM3D equipment has built-in active cooling system device, and the cylinder full of materials can be replaced within 5 hours of active cooling, which can save as many as 5 hours of cooling time compared with similar SLS equipment in China. For an example, to print a part as high as 150mm or less, TPM3D replace the material cylinder for a secondary print within just one hour of cooling time. TPM3D equipment greatly shortens the heating and cooling time of the powder, which can reduce the development costs of prototype manufacturers.
Fourth Efficiency: Consumables ---- Material Efficiency
TPM3D has paid great efforts on development of printing materials. In February 2018, TPM3D specially introduced several types of hybrid materials with high reuse rate. The reuse rate of old powder is as high as 95% and the cost of new powder can be reduced as low as 20%. There are many types of materials with high reuse rate, including the nylon 6/11/12 with complete functions as well as the aluminum powder/glass fiber hybrid nylon materials (please refer to the detailed material descriptions in following charters). The independently developed TPU and PEEK even fill the gap in the supply of all sintering plastic powders.
Fifth Efficiency: Power ---- Electricity Efficiency
TPM3D equipment has strong stability and low power consumption. The power consumption per hour is only 8KW, which is almost 50% lower than that of the similar 15KW equipment in the market. In the case of 12 working hours per day and 1 yuan of kilowatt-hour, the annual electricity consumption for the similar SLS equipment in the market is 65,700 yuan, while TPM3D equipment only cost 35,040 yuan, which can save as much as 30,660 yuan. Very impressively, the operation hours of many prototype manufacturers' 3D printing devices are far more than that, so the resulting benefits are obvious.
According to the Five Efficiencies introduced aforesaid, we’d like to make a summary based on the application data of TPM3D S360 printing equipment. S360 covers an area of 2*1.3m=2.6m2, the effective molding volume is 0.35*0.35*0.59=0.0722m3, the total powder consumption is 33.6kg. According to the proportion of 20% new powder, the price of 450 yuan/kg and printing height of 0.12mm, we can draw the conclusion that the price per millimeter is 5.4 yuan while that of other similar equipment is 8.16 yuan, about 150% of material cost difference. So, why are you still hesitating now? Come to join TPM3D’s customized money-saving team right now. There’s nothing we cannot make and we will bring unexpected surprises for you!
Some people may wonder how the cost of expensive prototype manufacturing be greatly reduced. Now, we’d like to make detailed explanation as follows!
First Efficiency: Equipment ---- Space efficiency
Firstly, with nearly 20 years of prototype service experience and technology, TPM3D can meet the customer's economic efficiency as much as possible during the continuous equipment improvement. Due to compact equipment structure, the cost of occupied space will be greatly reduced. The main host only takes 2.6m2of area, compared to the 3.7m2 of space occupation of other similar products. In China where factory space is very expensive, the cost of equipment space occupation is also an issue worth of being considered.
Second Efficiency: Powder Feeding ---- Time Efficiency
As for the design of powder feeding of sintering device, the mode of bilateral powder feeding with scrapers is adopted, which not only shortens the speed of powder feeding, but also saves the consumption of nitrogen as well as electricity. The oxidation rate of materials in high temperature environment has also be reduced to make powder quality more stable and less costs of use.
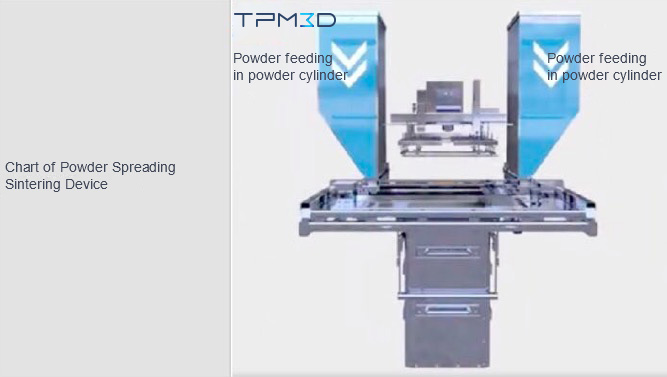
Third Efficiency: Scanning ---- Labor Efficiency
Due to Iradion Laser CO2, the scanning speed of TPM3D equipment can reach 15 m/s while the products of other brands can only reach 10 m/s and the light spot diameter can reach 0.3mm. With the built-in structure for constant temperature in same chamber, it can perform online compensation in single-point temperature detection while increasing powder heating speed. In addition, the TPM3D equipment has built-in active cooling system device, and the cylinder full of materials can be replaced within 5 hours of active cooling, which can save as many as 5 hours of cooling time compared with similar SLS equipment in China. For an example, to print a part as high as 150mm or less, TPM3D replace the material cylinder for a secondary print within just one hour of cooling time. TPM3D equipment greatly shortens the heating and cooling time of the powder, which can reduce the development costs of prototype manufacturers.
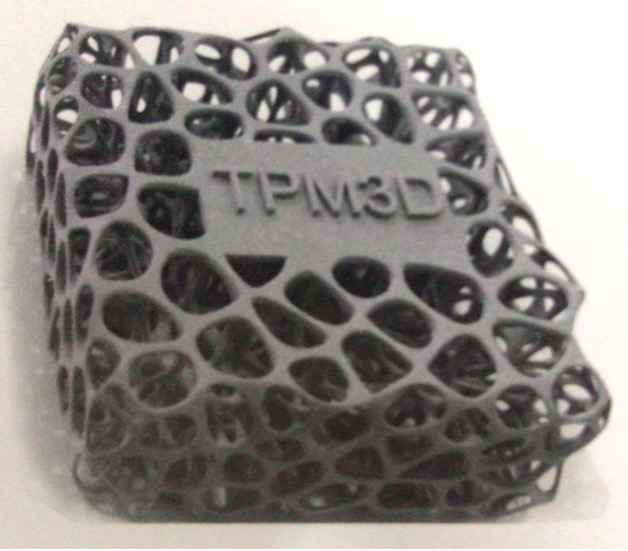
Fourth Efficiency: Consumables ---- Material Efficiency
TPM3D has paid great efforts on development of printing materials. In February 2018, TPM3D specially introduced several types of hybrid materials with high reuse rate. The reuse rate of old powder is as high as 95% and the cost of new powder can be reduced as low as 20%. There are many types of materials with high reuse rate, including the nylon 6/11/12 with complete functions as well as the aluminum powder/glass fiber hybrid nylon materials (please refer to the detailed material descriptions in following charters). The independently developed TPU and PEEK even fill the gap in the supply of all sintering plastic powders.
Fifth Efficiency: Power ---- Electricity Efficiency
TPM3D equipment has strong stability and low power consumption. The power consumption per hour is only 8KW, which is almost 50% lower than that of the similar 15KW equipment in the market. In the case of 12 working hours per day and 1 yuan of kilowatt-hour, the annual electricity consumption for the similar SLS equipment in the market is 65,700 yuan, while TPM3D equipment only cost 35,040 yuan, which can save as much as 30,660 yuan. Very impressively, the operation hours of many prototype manufacturers' 3D printing devices are far more than that, so the resulting benefits are obvious.

According to the Five Efficiencies introduced aforesaid, we’d like to make a summary based on the application data of TPM3D S360 printing equipment. S360 covers an area of 2*1.3m=2.6m2, the effective molding volume is 0.35*0.35*0.59=0.0722m3, the total powder consumption is 33.6kg. According to the proportion of 20% new powder, the price of 450 yuan/kg and printing height of 0.12mm, we can draw the conclusion that the price per millimeter is 5.4 yuan while that of other similar equipment is 8.16 yuan, about 150% of material cost difference. So, why are you still hesitating now? Come to join TPM3D’s customized money-saving team right now. There’s nothing we cannot make and we will bring unexpected surprises for you!