We first saw the combination of automobile and 3D printing was in the concept car. But now, 3D printing technology runs through the links of automobile R & D, trial production, production line fixture and jig, customized refit, and mass production.
A car can be simply divided into these major parts: engine, chassis, body, electrical equipment, which the number of their parts is up to 10,000-20,000. According to the type of material, it can be roughly divided into metal and non-metal. Non-metallic materials are mainly used in the interior trim, exterior trim, seals, tires and other parts of the vehicle.
At the stage of vehicle design and R&D, if only size and assembly verification are considered, almost all non-precision parts on vehicles can be manufactured by 3D printing technology and meet the requirements of verification. However, in order to realize functional verification, mass products and final use, the types of replacement parts for 3D printing manufacturing will be reduced due to the limitations of materials and processes. With the development of technology, there are more and more chemical reactions between 3D printing and automobile industry, which more and more new applications can be seen.
Founded in 1999, TPM3D Specializes in SLS 3D printing equipment R & D and manufacturing, material development, and provides 3D printing services.Thanks for years accumulation, TPM3D becomes a well-known brand in China, successfully developed S-series and P-series laser sintering additive manufacturing systems and a number of special high-reusability powders for different industries.
In the automobile industrial, Dongfeng Motor Group adopts SLS technology to print prototype parts during the trial production of new cars, including the central control panel printed with TPM3D's Precimid1172Pro GF30 BLK material, which is 30% glass reinforced nylon 12 material with excellent strength and impact resistance. And the distribution box shell printed with Precimid1172Pro material, which is a general nylon 12 material with good comprehensive performance and surface quality. After using 3D printing technology, Dongfeng Automobile can avoid the injection molding or machining process required by the manufacture of plastic parts, simplify the manufacturing process of prototype parts, and reduce the cost of outsourcing and the risk of model leakage.
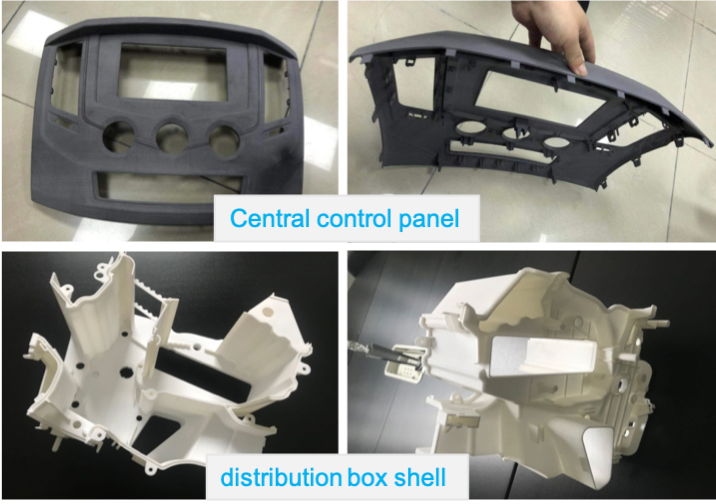
In addition, GAC Group also focuses on the application of SLS technology in the field of R & D and trial production, but its application is wider. The printed parts cover the range of the interior and exterior decoration, heat exchange system, power assembly, chassis and other parts of the vehicle, which can be used in the four major verification work including appearance, structure, installation and ergonomics, up to dozens of categories. In the past, the process of subcontracting included: demand submission, expense application, inquiry, delivery, receipt and acceptance. The cycle was usually 2-3 weeks. After the SLS 3D printing equipment was put into production, the process was shortened to 4 steps: demand submission, processing, receipt and acceptance. The verification work could be started in 4 days at the soonest, and the process was all within the company.
The above is only what we see at this stage. In the era of rapid development of technology, we believe that the application of 3D printing technology in the automotive industry will also develop in proportion.
So "car + 3D printing" should be equal to the present as well as the future!