Vorwort
Die Hauptkomponente des Strahlentherapiesystems ist der medizinische Elektronenlinearbeschleuniger, ein großes medizinisches Gerät, das Mikrowellenfelder verwendet, um Elektronen zu beschleunigen, um hochenergetische Strahlen zu erzeugen, und für externe Strahlentherapieaktivitäten über große Entfernungen in der menschlichen medizinischen Praxis verwendet wird. Es ist weit verbreitet in verschiedenen Die Behandlung von verschiedenen Tumoren, insbesondere die Behandlung von tiefen Tumoren. Medizinische Elektronen-Linearbeschleuniger können Röntgen- und/oder Elektronenstrahlungsstrahlen erzeugen. Hochenergetische Röntgenstrahlen haben die Eigenschaften einer hohen Durchdringung, einer niedrigen Hautdosis und einer hohen Strahlengleichmäßigkeit und eignen sich zur Behandlung tiefer Tumore. Elektronenstrahlen haben bestimmte Reichweiteneigenschaften und eine geringe Durchdringungsfähigkeit und werden zur Behandlung oberflächlicher Tumore eingesetzt. Das medizinische Behandlungsbett ist der Träger der Strahlentherapie des Patienten. Während des Strahlentherapieprozesses sollte der Einfluss des Bettbretts auf die Absorption der Strahlendosis berücksichtigt werden. Daher verwendet das aktuelle High-End-Behandlungsbettbrett keine Aluminiumlegierungsmaterialien mehr, um die Durchlässigkeit des Bettbretts für Röntgenstrahlen zu verbessern und die Dämpfung zu reduzieren.
Anwendung
Als kürzlich ein Krankenhaus das Elekta-Strahlentherapiesystem installierte, wurde festgestellt, dass eines der beiden Verbindungsteile des Kohlefaser-Behandlungsbetts iBeam evo Expansion Board während des Transports verloren ging. Der Originalverbinder wird im Kohlefaser-CNC-Fräsverfahren bearbeitet. Die Kosten für die Verarbeitung dieses Teils mit dem gleichen Material werden voraussichtlich 2.000 Yuan übersteigen, und der Verarbeitungszyklus ist aufgrund der Epidemie länger. Ohne diesen Anschluss kann die Bettstütze nicht erreicht werden. Es wird erwartet, dass sich die Funktion des Kopfes, der Fortschritt der Inbetriebnahme und Inbetriebnahme der Ausrüstung um mehr als 2 Monate verzögern wird. Auf der anderen Seite, obwohl der CNC-Bearbeitungszyklus der Aluminiumlegierung kurz und die Kosten niedrig sind, wirkt sich dies auf die Röntgendurchlässigkeit des Behandlungsbettes aus und beeinflusst dann die Verwendung des gesamten Gerätesatzes.
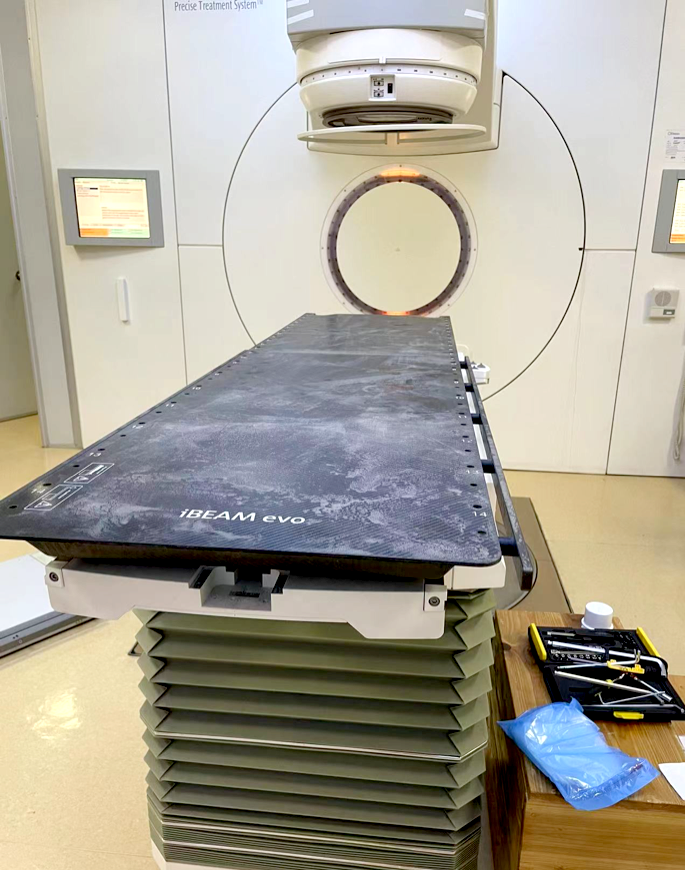
Abbildung 1: Das Strahlentherapiesystem und das Kohlefaser-Behandlungsbett werden im Krankenhaus installiert
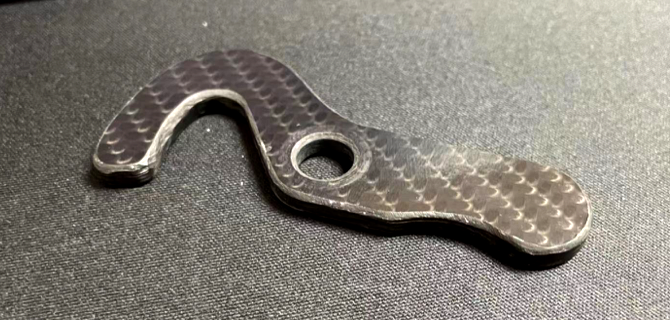
Abbildung 2: Der ursprüngliche Stecker auf der gegenüberliegenden Seite, der nicht verloren gegangen ist
Nach der Kommunikation entschied sich das Krankenhaus schließlich, mit TPM3D zusammenzuarbeiten, wobei 3D-Scanning, Reverse Design und3D-Drucker Lasersintern, Verwendung von Nylonmaterialien, um diesen Steckverbinder schnell anzupassen, während der Produktionszyklus beschleunigt und die Produktionskosten gesenkt werden, hat dies keinen Einfluss auf das Behandlungsbett. Die Durchdringungsrate der Röntgenstrahlen gewährleistet den Fortschritt des Gerätebetriebs.
Da zunächst keine Modelldaten vorhanden sind, ist es notwendig, das andere Verbindungsstück auf der gegenüberliegenden Seite zu verwenden, um ein 3D-Modell durch 3D-Scannen und umgekehrtes Design zu erhalten. Da die Struktur dieses Stücks relativ einfach ist, sind die Scan- und Rückwärtsgeschwindigkeit schnell und die Datenvorbereitung ist innerhalb von 2 Stunden abgeschlossen.
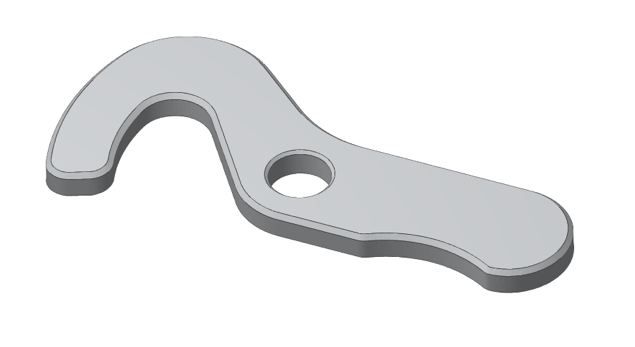
Abbildung 3: Daten nach 3D-Scanning und Reverse Design
Nachdem wir die 3D-Daten der angeschlossenen Teile erhalten hatten, arrangierten wir sofort die Druckaufgabe. Nachdem wir die Nutzungsanforderungen dieses Steckverbinders bewertet hatten, entschieden wir uns schließlich für das Precimid1172Pro BLK Nylon 12-Material für den Druck. Dies ist ein schwarzes Nylonpolymermaterial mit hervorragender umfassender Leistung. Es hat eine gute mechanische Festigkeit und Verschleißfestigkeit und Haltbarkeit, die diese Anwendung erfüllen kann. Der Nutzungsbedarf in der Szene und die Materialwiederverwendungsrate ist hoch und die Wirtschaftlichkeit gut. Das Druckmodell ist TPM3D P360, das eine hohe Druckgeschwindigkeit und hohe Stabilität aufweist und sowohl die Formgröße als auch die Produktionseffizienz aufweist. In Zusammenarbeit mit dem One-Stop-Teile-Pulver-Full-Performance-Verarbeitungsarbeitsplatz (PPS) kann eine automatische Online-Pulverversorgung realisiert werden, um den Anforderungen an kontinuierliche Produktion und Umweltfreundlichkeit gerecht zu werden.
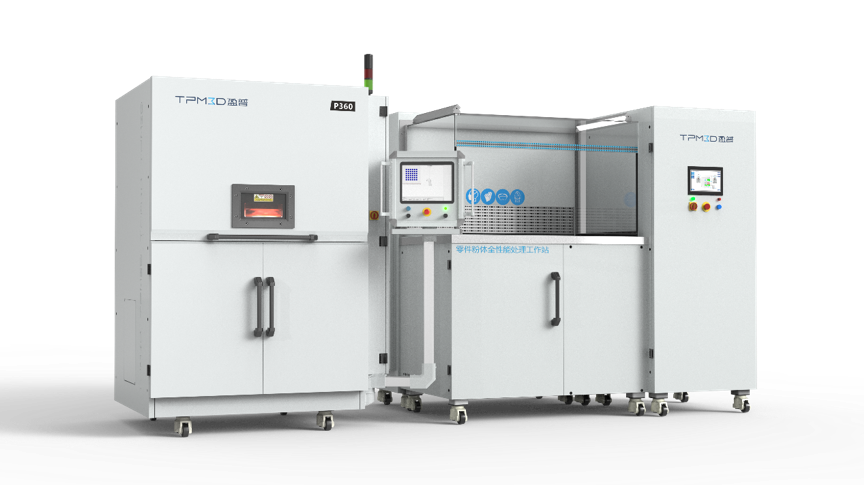
Abbildung 4: Saubere Produktionslösung TPM3D P360
Nach dem Drucken, Kühlen und Reinigen von Pulver führten wir eine Nachbehandlung der chemischen Dampfglättungstechnologie an dieser Verbindung durch, um die Oberfläche des Teils glatter zu machen und seine Festigkeit und Haltbarkeit zu verbessern. Die chemische Dampfglättungstechnologie verwendet ein spezielles chemisches Lösungsmittel, um die Teile in der Kabine nach dem Verdampfen zu begasen, wodurch die Oberfläche der Teile "geglättet" wird, wodurch die Oberfläche glatt, dicht, wasserdicht und antifouling wird. Darüber hinaus wird dank der Verringerung der Oberflächenrauheit des Teils und des Verschwindens des Risspunkts seine Zähigkeit deutlich verbessert und es ist haltbarer.
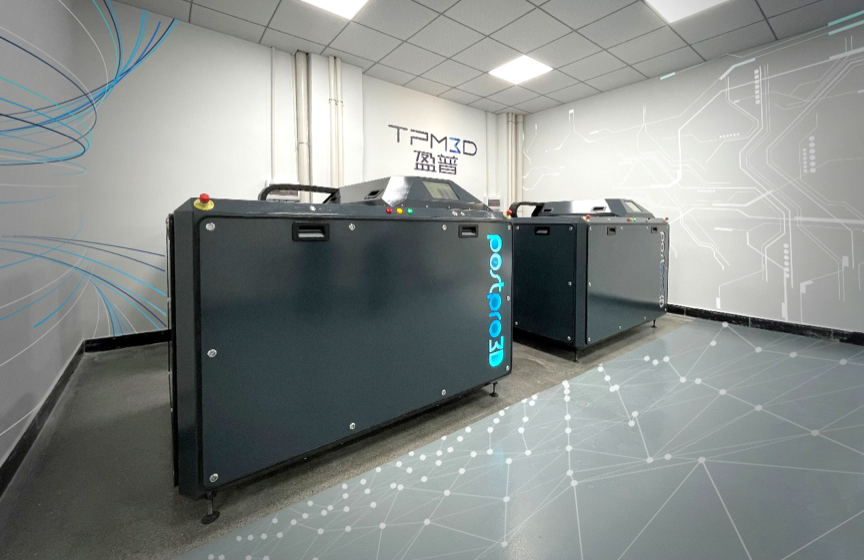
Abbildung 5: TPM3D ist das erste Unternehmen, das die chemische Dampfpoliertechnologie AMT in China einführt
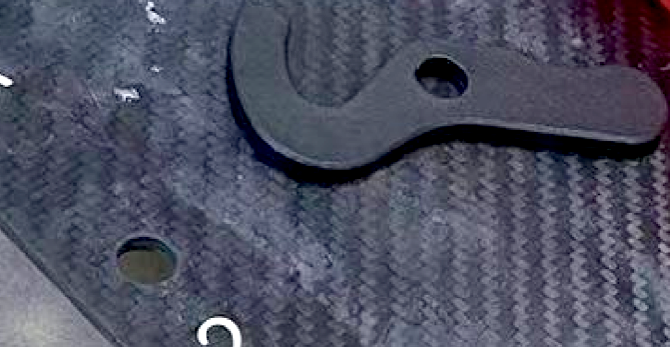
Abbildung 6: SLS-Nylon-Druckanschlüsse werden installiert
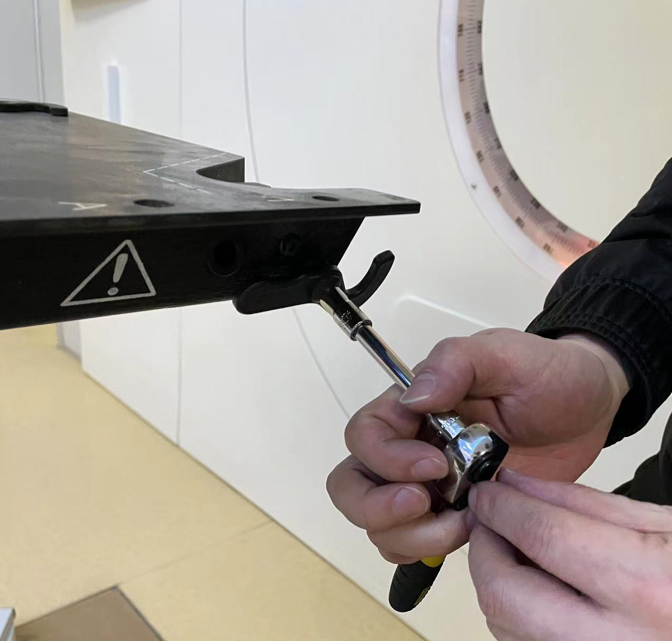
Abbildung 7: SLS-Nylon-Druckanschlüsse werden installiert
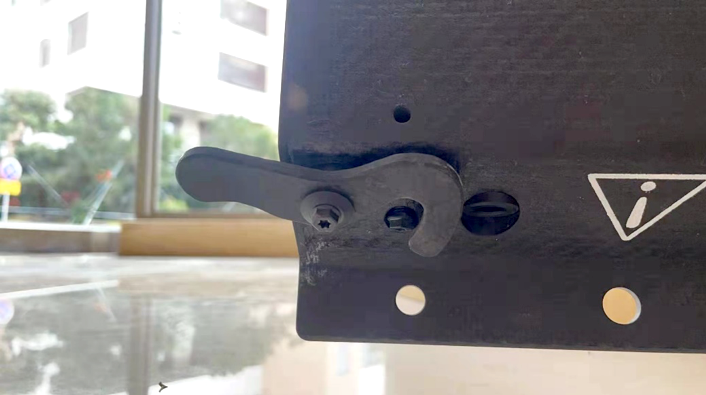
Abbildung 8: Installierter SLS-Druckanschluss und Erweiterungsplatine
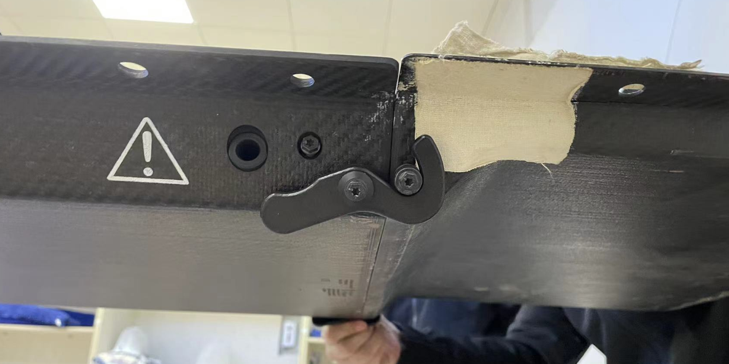
Abbildung 9: SLS-Druckanschluss und Erweiterungsplatine nach der Installation
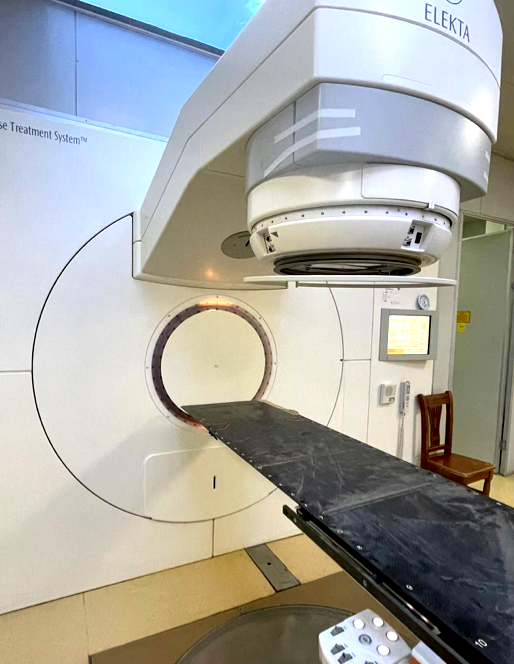
Abbildung 10: Systeminstallation und Inbetriebnahme abgeschlossen und einsatzbereit
In Anbetracht der geringen Größe des Teils und der "kombinierten Topfmethode", die im eigentlichen Verarbeitungsprozess zum Drucken und Räuchern und Polieren zusammen mit anderen Aufträgen verwendet wird, betragen die tatsächlichen Verarbeitungskosten weniger als 400 Yuan. Es dauert 1 Tag, was dem Krankenhaus Geldkosten und viel Zeitkosten spart, die Installation und Inbetriebnahme so schnell wie möglich durchführen kann und den Zeitknoten garantiert, an dem die Strahlentherapiegeräte in Betrieb genommen werden sollen. Es wurde erneut bestätigt, dass die SLS-Lasersintertechnologie sehr gut für die Herstellung und Herstellung von Kleinserien kundenspezifischer Endteile geeignet ist und über eine schnelle Reaktion und flexible Fertigung verfügt.
Die Hauptkomponente des Strahlentherapiesystems ist der medizinische Elektronenlinearbeschleuniger, ein großes medizinisches Gerät, das Mikrowellenfelder verwendet, um Elektronen zu beschleunigen, um hochenergetische Strahlen zu erzeugen, und für externe Strahlentherapieaktivitäten über große Entfernungen in der menschlichen medizinischen Praxis verwendet wird. Es ist weit verbreitet in verschiedenen Die Behandlung von verschiedenen Tumoren, insbesondere die Behandlung von tiefen Tumoren. Medizinische Elektronen-Linearbeschleuniger können Röntgen- und/oder Elektronenstrahlungsstrahlen erzeugen. Hochenergetische Röntgenstrahlen haben die Eigenschaften einer hohen Durchdringung, einer niedrigen Hautdosis und einer hohen Strahlengleichmäßigkeit und eignen sich zur Behandlung tiefer Tumore. Elektronenstrahlen haben bestimmte Reichweiteneigenschaften und eine geringe Durchdringungsfähigkeit und werden zur Behandlung oberflächlicher Tumore eingesetzt. Das medizinische Behandlungsbett ist der Träger der Strahlentherapie des Patienten. Während des Strahlentherapieprozesses sollte der Einfluss des Bettbretts auf die Absorption der Strahlendosis berücksichtigt werden. Daher verwendet das aktuelle High-End-Behandlungsbettbrett keine Aluminiumlegierungsmaterialien mehr, um die Durchlässigkeit des Bettbretts für Röntgenstrahlen zu verbessern und die Dämpfung zu reduzieren.
Anwendung
Als kürzlich ein Krankenhaus das Elekta-Strahlentherapiesystem installierte, wurde festgestellt, dass eines der beiden Verbindungsteile des Kohlefaser-Behandlungsbetts iBeam evo Expansion Board während des Transports verloren ging. Der Originalverbinder wird im Kohlefaser-CNC-Fräsverfahren bearbeitet. Die Kosten für die Verarbeitung dieses Teils mit dem gleichen Material werden voraussichtlich 2.000 Yuan übersteigen, und der Verarbeitungszyklus ist aufgrund der Epidemie länger. Ohne diesen Anschluss kann die Bettstütze nicht erreicht werden. Es wird erwartet, dass sich die Funktion des Kopfes, der Fortschritt der Inbetriebnahme und Inbetriebnahme der Ausrüstung um mehr als 2 Monate verzögern wird. Auf der anderen Seite, obwohl der CNC-Bearbeitungszyklus der Aluminiumlegierung kurz und die Kosten niedrig sind, wirkt sich dies auf die Röntgendurchlässigkeit des Behandlungsbettes aus und beeinflusst dann die Verwendung des gesamten Gerätesatzes.
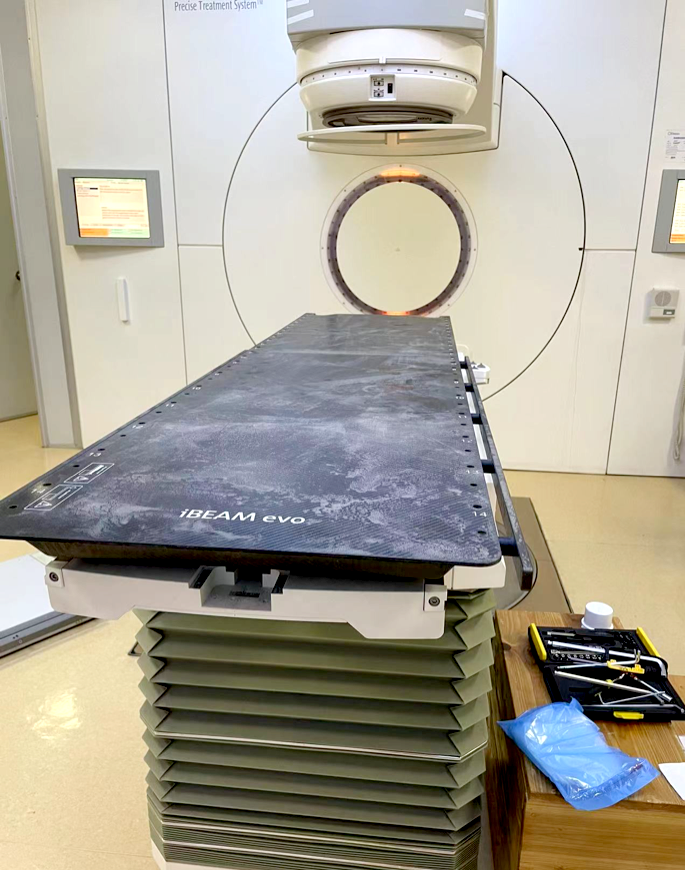
Abbildung 1: Das Strahlentherapiesystem und das Kohlefaser-Behandlungsbett werden im Krankenhaus installiert
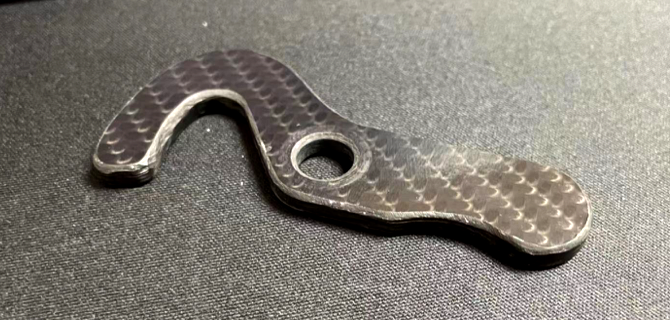
Abbildung 2: Der ursprüngliche Stecker auf der gegenüberliegenden Seite, der nicht verloren gegangen ist
Nach der Kommunikation entschied sich das Krankenhaus schließlich, mit TPM3D zusammenzuarbeiten, wobei 3D-Scanning, Reverse Design und3D-Drucker Lasersintern, Verwendung von Nylonmaterialien, um diesen Steckverbinder schnell anzupassen, während der Produktionszyklus beschleunigt und die Produktionskosten gesenkt werden, hat dies keinen Einfluss auf das Behandlungsbett. Die Durchdringungsrate der Röntgenstrahlen gewährleistet den Fortschritt des Gerätebetriebs.
Da zunächst keine Modelldaten vorhanden sind, ist es notwendig, das andere Verbindungsstück auf der gegenüberliegenden Seite zu verwenden, um ein 3D-Modell durch 3D-Scannen und umgekehrtes Design zu erhalten. Da die Struktur dieses Stücks relativ einfach ist, sind die Scan- und Rückwärtsgeschwindigkeit schnell und die Datenvorbereitung ist innerhalb von 2 Stunden abgeschlossen.
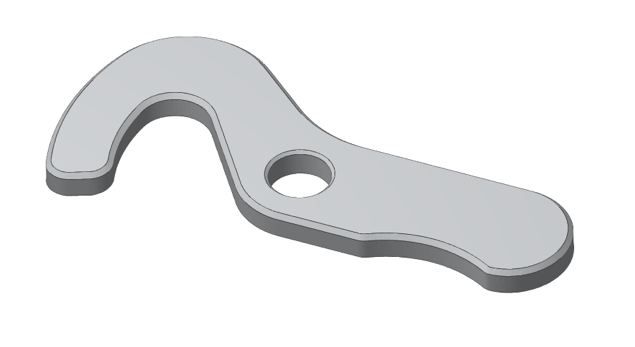
Abbildung 3: Daten nach 3D-Scanning und Reverse Design
Nachdem wir die 3D-Daten der angeschlossenen Teile erhalten hatten, arrangierten wir sofort die Druckaufgabe. Nachdem wir die Nutzungsanforderungen dieses Steckverbinders bewertet hatten, entschieden wir uns schließlich für das Precimid1172Pro BLK Nylon 12-Material für den Druck. Dies ist ein schwarzes Nylonpolymermaterial mit hervorragender umfassender Leistung. Es hat eine gute mechanische Festigkeit und Verschleißfestigkeit und Haltbarkeit, die diese Anwendung erfüllen kann. Der Nutzungsbedarf in der Szene und die Materialwiederverwendungsrate ist hoch und die Wirtschaftlichkeit gut. Das Druckmodell ist TPM3D P360, das eine hohe Druckgeschwindigkeit und hohe Stabilität aufweist und sowohl die Formgröße als auch die Produktionseffizienz aufweist. In Zusammenarbeit mit dem One-Stop-Teile-Pulver-Full-Performance-Verarbeitungsarbeitsplatz (PPS) kann eine automatische Online-Pulverversorgung realisiert werden, um den Anforderungen an kontinuierliche Produktion und Umweltfreundlichkeit gerecht zu werden.
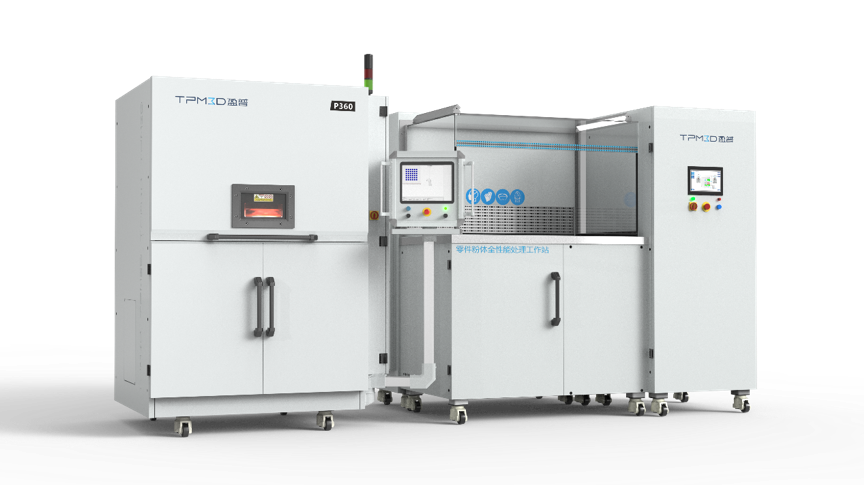
Abbildung 4: Saubere Produktionslösung TPM3D P360
Nach dem Drucken, Kühlen und Reinigen von Pulver führten wir eine Nachbehandlung der chemischen Dampfglättungstechnologie an dieser Verbindung durch, um die Oberfläche des Teils glatter zu machen und seine Festigkeit und Haltbarkeit zu verbessern. Die chemische Dampfglättungstechnologie verwendet ein spezielles chemisches Lösungsmittel, um die Teile in der Kabine nach dem Verdampfen zu begasen, wodurch die Oberfläche der Teile "geglättet" wird, wodurch die Oberfläche glatt, dicht, wasserdicht und antifouling wird. Darüber hinaus wird dank der Verringerung der Oberflächenrauheit des Teils und des Verschwindens des Risspunkts seine Zähigkeit deutlich verbessert und es ist haltbarer.
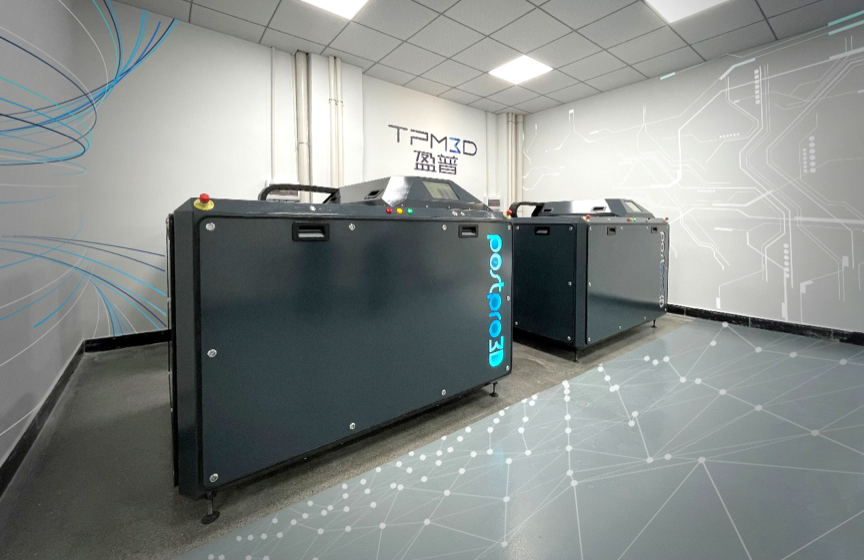
Abbildung 5: TPM3D ist das erste Unternehmen, das die chemische Dampfpoliertechnologie AMT in China einführt
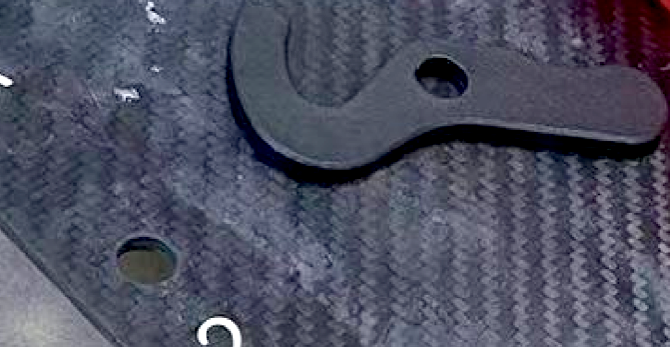
Abbildung 6: SLS-Nylon-Druckanschlüsse werden installiert
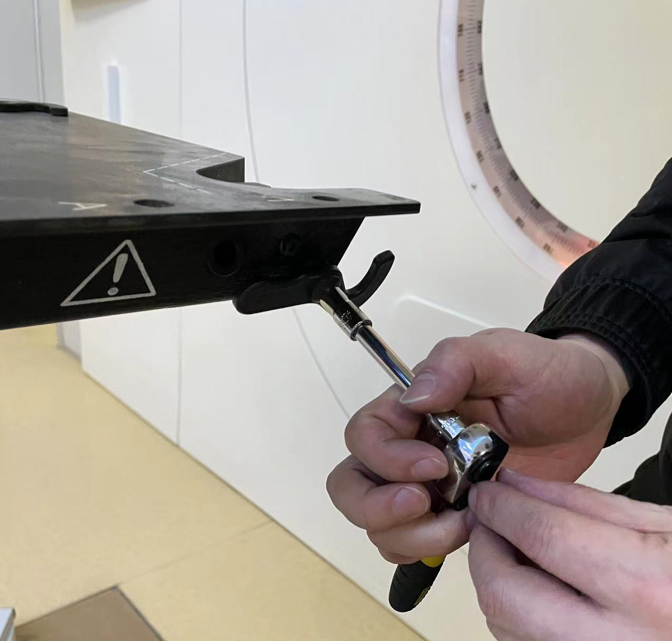
Abbildung 7: SLS-Nylon-Druckanschlüsse werden installiert
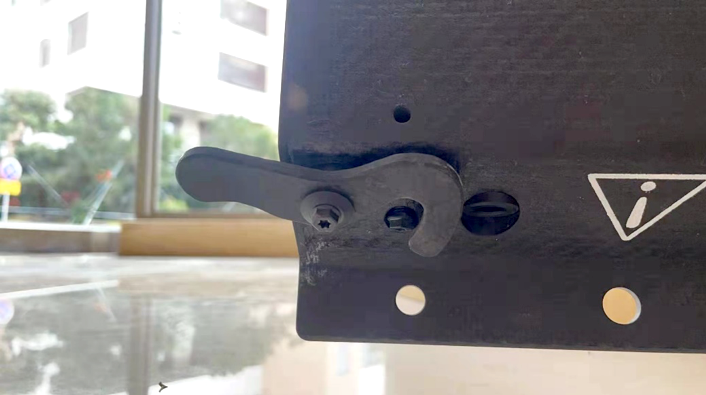
Abbildung 8: Installierter SLS-Druckanschluss und Erweiterungsplatine
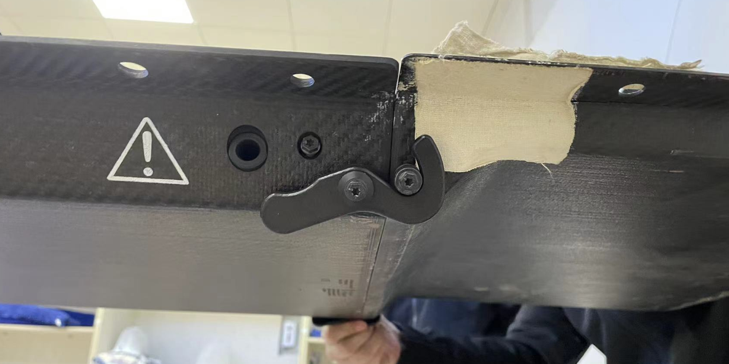
Abbildung 9: SLS-Druckanschluss und Erweiterungsplatine nach der Installation
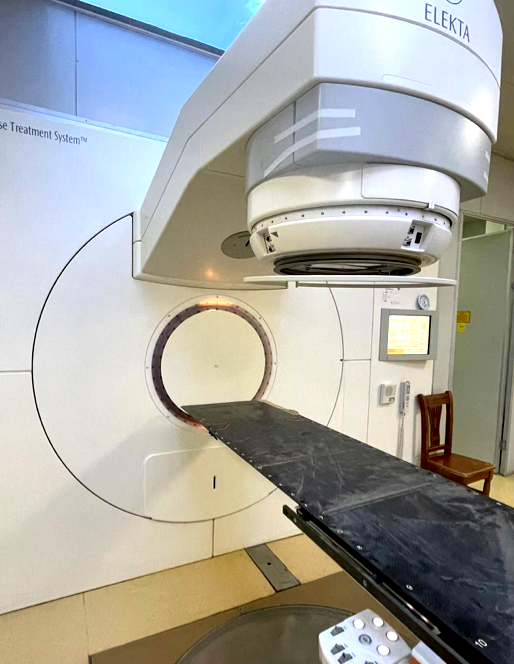
Abbildung 10: Systeminstallation und Inbetriebnahme abgeschlossen und einsatzbereit
In Anbetracht der geringen Größe des Teils und der "kombinierten Topfmethode", die im eigentlichen Verarbeitungsprozess zum Drucken und Räuchern und Polieren zusammen mit anderen Aufträgen verwendet wird, betragen die tatsächlichen Verarbeitungskosten weniger als 400 Yuan. Es dauert 1 Tag, was dem Krankenhaus Geldkosten und viel Zeitkosten spart, die Installation und Inbetriebnahme so schnell wie möglich durchführen kann und den Zeitknoten garantiert, an dem die Strahlentherapiegeräte in Betrieb genommen werden sollen. Es wurde erneut bestätigt, dass die SLS-Lasersintertechnologie sehr gut für die Herstellung und Herstellung von Kleinserien kundenspezifischer Endteile geeignet ist und über eine schnelle Reaktion und flexible Fertigung verfügt.