Elektrificatie en automatisering hebben zich snel ontwikkeld in China.Molded-case stroomonderbrekers (MCCB's) zijn op grote schaal gebruikt voor hun goede overbelastings- en kortsluitbeveiligingsfuncties.
1.Achtergrond:
Elektrificatie en automatisering hebben zich snel ontwikkeld in China.Molded-case stroomonderbrekers (MCCB's) zijn op grote schaal gebruikt voor hun goede overbelastings- en kortsluitbeveiligingsfuncties. MCCB's, als de meest elementaire beschermende apparaten, beschikken over uitgebreide toepassing, een breed scala aan variëteiten en een compacte en gecompliceerde structuur. In het verleden vonden ontwerpers en producenten van elektrische apparaten het vaak nodig om prototype-onderdelen te vervaardigen door middel van siliconencoatingverwerking en CNC-verwerking, en om verificatie en testen uit te voeren in de ontwerp- en ontwikkelingsfase van nieuwe producten, wat een lange verwerkingscyclus en hoge kosten zou vereisen en een groot probleem zou worden als er elk jaar tientallen of honderden nieuwe producten moesten worden ontwikkeld. Hieronder ziet u een case met een eindklant van TPM3D.
2.Customer profiel:
De klant is een wereldberoemde leverancier van slimme energieoplossingen en zijn producten omvatten stroomverdelers, terminalapparatuur, motorbesturings- en beveiligingsapparatuur, industriële automatisering, enz. Met een jaarlijkse omzet van meer dan RMB 80 miljard is het bedrijf actief in meer dan 140 landen en regio's. Deze klant combineert tpm3d P360 lasersintersysteem met PPS voor zijn R&D en proefproductie van diverse laagspanningstoestellen.
3.Productontwikkeling:
De klant ontwikkelt en produceert jaarlijks meer dan 10.000 nieuwe elektrische producten. Op dit moment omvatten de belangrijkste producten die zijn geprint met TPM3D P360 behuizingen voor stroomonderbrekers met gegoten behuizing en andere structurele onderdelen.
Nadat het monster is afgedrukt, voert de klant assemblageverificatie en functionele tests uit. De nauwkeurigheid van de assemblageverificatie is vereist om ± 0,2 mm te bereiken. De functionele tests omvatten voornamelijk: sterktetest, lange vertragingstest, isolatietest, enz. Het aangenomen materiaal is 30% glasparel versterkt nylon 12 (Precimid1172Pro GF30) van TMP3D, dat een uitstekende sterkte en slagvastheid heeft. Volgens de klant kunnen de materialen voldoen aan testeisen op het gebied van mechanische eigenschappen en isolatie. Bovendien bereikt de thermische vervormingstemperatuur van het materiaal zo hoog als 184,4 ° C en kunnen de geprinte behuizingen worden getest zonder gedurende 4 uur in een thermostaat bij 80 ° C te worden vervormd, wat voldoet aan de vereisten van de lange vertragingstest. Over het algemeen zijn gevallen van gegoten stroomonderbrekers bedrukt met SLS-technologie vergelijkbaar met traditionele spuitgietonderdelen.
4.Milieuvriendelijk:
Bij de aankoop van het P360 lasersintersysteem heeft de klant ook een Parts & Powder Processing Station (PPS) geconfigureerd, dat in 2018 door TPM3D werd gelanceerd, de eerste in Azië, onderdelenreiniging, poederrecycling, mengen, voeren en poeder verzamelen integreerde, loste de problemen op zoals tijdverspilling, vervuiling en veiligheid bij arbeidsbedrijf. PPS heeft de nationale norm voor stofexplosiebestendige zone 22 en de internationale CE-certificering doorstaan en heeft hoge erkenning gekregen voor zijn betere prestaties bij het waarborgen van de veiligheid van de gebruiker.
5.Kostenreductie en efficiëntieverbetering:
Voordat het SLS 3D-printsysteem werd geïntroduceerd, nam de klant CNC-bewerking of uitbestede siliconencoatingbewerking over, wat minstens 5-6 dagen duurde om de testonderdelen te verkrijgen. Nadat het P360 lasersintersysteem in productie was genomen, konden monsters al na 48 uur worden verkregen en getest, waardoor meer dan 60% tijd werd bespaard. In het verleden kostte uitbestede caseverwerking ongeveer RMB 4.000 / set. Met SLS 3D-printtechnologie kunnen de kosten worden beheerst onder RMB 700/set, een besparing van meer dan 80%. Met een hoge bezettingsgraad kan de apparatuur van de klant momenteel gemiddeld 2-3 volledige kamer per week afdrukken. Bovendien kan het volgens de klant ongeveer RMB 700.000 per jaar besparen, waardoor de kosten beter worden verlaagd en de efficiëntie wordt verbeterd.
Vergelijking van kosten en cyclus tussen traditioneel proces en SLS 3D-printproces:
"TPM3D's P360-systeem is handig en snel; PPS vermindert handmatige interventie en bereikt een hoge verwerkingsefficiëntie van onderdelen en poeder. De oplossing bespaart tijd en kosten en zorgt voor netheid en veiligheid van het milieu."
——Feedback van de klant
Elektrificatie en automatisering hebben zich snel ontwikkeld in China.Molded-case stroomonderbrekers (MCCB's) zijn op grote schaal gebruikt voor hun goede overbelastings- en kortsluitbeveiligingsfuncties. MCCB's, als de meest elementaire beschermende apparaten, beschikken over uitgebreide toepassing, een breed scala aan variëteiten en een compacte en gecompliceerde structuur. In het verleden vonden ontwerpers en producenten van elektrische apparaten het vaak nodig om prototype-onderdelen te vervaardigen door middel van siliconencoatingverwerking en CNC-verwerking, en om verificatie en testen uit te voeren in de ontwerp- en ontwikkelingsfase van nieuwe producten, wat een lange verwerkingscyclus en hoge kosten zou vereisen en een groot probleem zou worden als er elk jaar tientallen of honderden nieuwe producten moesten worden ontwikkeld. Hieronder ziet u een case met een eindklant van TPM3D.
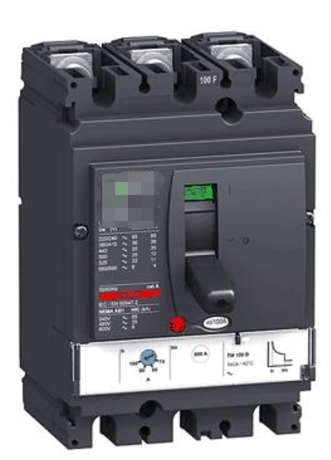
Een soort gegoten kast stroomonderbreker
2.Customer profiel:
De klant is een wereldberoemde leverancier van slimme energieoplossingen en zijn producten omvatten stroomverdelers, terminalapparatuur, motorbesturings- en beveiligingsapparatuur, industriële automatisering, enz. Met een jaarlijkse omzet van meer dan RMB 80 miljard is het bedrijf actief in meer dan 140 landen en regio's. Deze klant combineert tpm3d P360 lasersintersysteem met PPS voor zijn R&D en proefproductie van diverse laagspanningstoestellen.

TPM3D P360 Laser Sintering Systeem +PPS
3.Productontwikkeling:
De klant ontwikkelt en produceert jaarlijks meer dan 10.000 nieuwe elektrische producten. Op dit moment omvatten de belangrijkste producten die zijn geprint met TPM3D P360 behuizingen voor stroomonderbrekers met gegoten behuizing en andere structurele onderdelen.

gegoten stroomonderbreker ontwikkeld door SLS-technologie
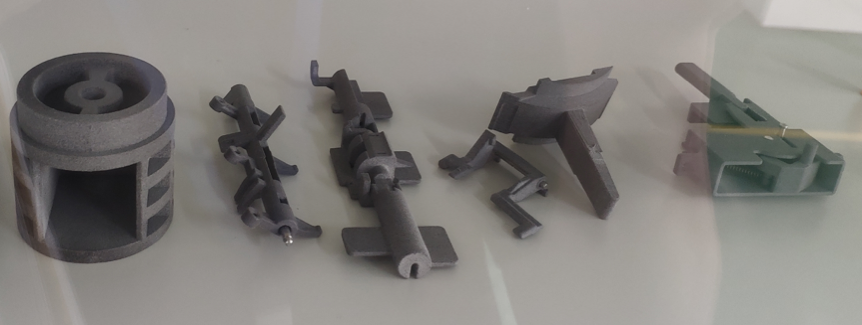
Andere structurele onderdelen
Nadat het monster is afgedrukt, voert de klant assemblageverificatie en functionele tests uit. De nauwkeurigheid van de assemblageverificatie is vereist om ± 0,2 mm te bereiken. De functionele tests omvatten voornamelijk: sterktetest, lange vertragingstest, isolatietest, enz. Het aangenomen materiaal is 30% glasparel versterkt nylon 12 (Precimid1172Pro GF30) van TMP3D, dat een uitstekende sterkte en slagvastheid heeft. Volgens de klant kunnen de materialen voldoen aan testeisen op het gebied van mechanische eigenschappen en isolatie. Bovendien bereikt de thermische vervormingstemperatuur van het materiaal zo hoog als 184,4 ° C en kunnen de geprinte behuizingen worden getest zonder gedurende 4 uur in een thermostaat bij 80 ° C te worden vervormd, wat voldoet aan de vereisten van de lange vertragingstest. Over het algemeen zijn gevallen van gegoten stroomonderbrekers bedrukt met SLS-technologie vergelijkbaar met traditionele spuitgietonderdelen.
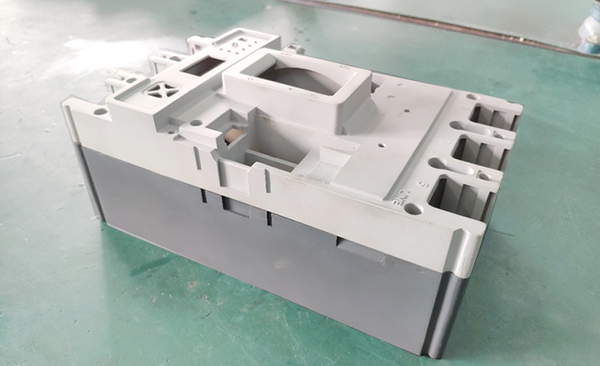
Montage verificatie
4.Milieuvriendelijk:
Bij de aankoop van het P360 lasersintersysteem heeft de klant ook een Parts & Powder Processing Station (PPS) geconfigureerd, dat in 2018 door TPM3D werd gelanceerd, de eerste in Azië, onderdelenreiniging, poederrecycling, mengen, voeren en poeder verzamelen integreerde, loste de problemen op zoals tijdverspilling, vervuiling en veiligheid bij arbeidsbedrijf. PPS heeft de nationale norm voor stofexplosiebestendige zone 22 en de internationale CE-certificering doorstaan en heeft hoge erkenning gekregen voor zijn betere prestaties bij het waarborgen van de veiligheid van de gebruiker.

schone en nette omgeving
5.Kostenreductie en efficiëntieverbetering:
Voordat het SLS 3D-printsysteem werd geïntroduceerd, nam de klant CNC-bewerking of uitbestede siliconencoatingbewerking over, wat minstens 5-6 dagen duurde om de testonderdelen te verkrijgen. Nadat het P360 lasersintersysteem in productie was genomen, konden monsters al na 48 uur worden verkregen en getest, waardoor meer dan 60% tijd werd bespaard. In het verleden kostte uitbestede caseverwerking ongeveer RMB 4.000 / set. Met SLS 3D-printtechnologie kunnen de kosten worden beheerst onder RMB 700/set, een besparing van meer dan 80%. Met een hoge bezettingsgraad kan de apparatuur van de klant momenteel gemiddeld 2-3 volledige kamer per week afdrukken. Bovendien kan het volgens de klant ongeveer RMB 700.000 per jaar besparen, waardoor de kosten beter worden verlaagd en de efficiëntie wordt verbeterd.
Vergelijking van kosten en cyclus tussen traditioneel proces en SLS 3D-printproces:
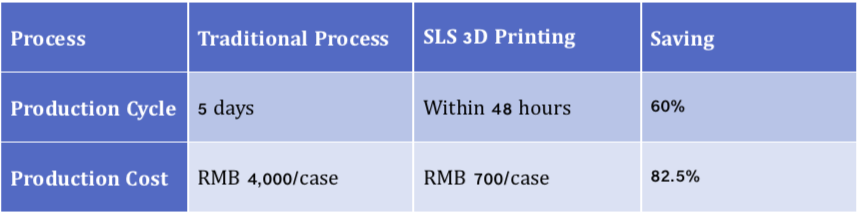
"TPM3D's P360-systeem is handig en snel; PPS vermindert handmatige interventie en bereikt een hoge verwerkingsefficiëntie van onderdelen en poeder. De oplossing bespaart tijd en kosten en zorgt voor netheid en veiligheid van het milieu."
——Feedback van de klant